300 series stainless tig welding due to its long-term cost effectiveness and inherent corrosion resistance, austenitic stainless steel has
300 Series Stainless Tig Welding
Due to its long-term cost effectiveness and inherent corrosion
resistance, austenitic stainless steel has become a staple material
across many industries. Also known as 300 series, austenitic stainless
steel poses distinct challenges when TIG welded, the greatest of which
are carbide precipitation and distortion. The key to preventing these
pitfalls is good heat control, correct travel speeds and adequate gas
coverage.
Austenitic Stainless Steel Basics:
By its very nature, austenitic stainless steel is a poor conductor of
heat. The presence of nickel (6-22%), along with chromium (16-26%),
enhances its corrosion and/or stain resistance, but these and other
elements—often titanium or molybdenum—also cause it to react to heat
differently than other materials. Effectively, austenitic stainless
steel conducts heat at around half the rate of mild steel, but has a
much higher rate of thermal expansion when welded.
Good heat control, gas coverage and
travel speeds can help ensure TIG
welding success on stainless steel.
Typically, austenitic stainless steel requires a DC power source and
pointed tungsten (any type except pure) to TIG weld it. Like aluminum,
it should be free of oil, paint and/or dirt prior to welding to
achieve optimal results. Unlike aluminum, however, austenitic
stainless steel does not require wire brushing prior to welding.
Instead, the material should be wire brushed between welding passes
with a stainless steel wire brush that has not had contact with steel
to help remove potential interpass oxides.
Filler rod is recommended on applications with a base material thicker
than gauge 18 and will be contingent upon joint design. For example,
outside corners may not require filler rod, but an inside joint will.
Most TIG applications require overmatching of the filler rod. That is,
a filler rod with higher strength properties should be used. For
example, on 304 series austenitic stainless steel, an ER308 rod should
be used. Typically, austenitic stainless steel filler rods are
available in diameters ranging from .035 to 5/32 (.9-to 4.0-mm) and
chosen according to the joint design, welding parameters and
applications.
Filler Rod Selection.
Stainless Steel
Filler Rod Used
Stainless Steel
Filler Rod Used
301
308
310S
310
302
308
314
310, 312
302S
308
316
316
304
308
316L
316
304L
308
317
347
305
308, 310
321
347
308
308
330
347
309
309
347
347
309S
309
348
347, 348
310
310
What is Carbide Precipitation?
Carbide precipitation occurs when the chrome and carbon in the
austenitic stainless steel is drawn out of the material and reacts to
the atmosphere. It occurs between 800 to 1400 degrees Fahrenheit (426
to 760 degrees Celsius), so care should be taken to keep the weld zone
below that range or in an inert atmosphere (via argon shielding gas).
Because austenitic stainless steel is easily readable when welded—a
good weld is straw colored. It is equally easy to detect when carbide
precipitation has occurred: the austenitic stainless steel will turn
black. When carbide precipitation is present: the material will turn
blue or purple after being TIG welded.
There are three causes of carbide precipitation: heat, travel speed
and gas. Specifically, too hot of a TIG weld, too slow of travel speed
and/or inadequate shielding gas coverage can individually, or in
combination, cause the problem.
Heat and Travel Speed.
The best defense against carbide precipitation is practice and a few
key guidelines.
1) The rule of amperages: unlike the rule for steel, stainless steel
requires 1/3rd less amps for every thousandths of an inch of material
thickness.
2) Maintaining an appropriate travel speed helps prevent an excess
amount of heat from entering the TIG weld.
3) Choosing the correct tungsten diameter and grind on the tip. See
page 7.
Aside from practice, one way to monitor travel speed is to look for
what is dubbed the “devil’s eye.” The “devil’s eye” is a fluid dot in
the center of the weld puddle that is formed by foreign elements that
continuously dance around in the center of the weld puddle. The
presence of the “devil’s eye” is insurance that not only is travel
speed appropriate, but also that other factors like torch angle,
filler rod position, penetration and root opening are all optimal. As
you are welding try to keep the HAZ as narrow as possible while still
maintaining good penetration.
Many people hold their breath in an effort to become steadier or they
hold too tightly on to the torch. Relax and breathe normally while
maintain a gently grip on the torch. This will avoid hand fatigue and
shaking while welding.
Gas Coverage.
Using the appropriate type and amount of shielding gas is another
important way to prevent carbide precipitation. Typically, pure argon
provides the best results when welding thinner austenitic stainless
steel, but the addition of small percentages of hydrogen is not
uncommon when faster travel speeds are desired, especially on thicker
pieces or in automated application. The average flow required is
between 15 to 20 psi, anything greater will cause turbulence in the
gas flow and weld puddle and result in a poor weld.
The use of a gas lens is highly recommended when TIG welding
austenitic stainless steel. A gas lens is a copper and brass component
with layered stainless steel mesh screens that replaces the collet
body in a standard GTAW torch. The gas lens helps distribute gas more
evenly around the tungsten, arc and weld puddle and provides good
cooling action.
Full penetration welds require back purging. Covering the back of the
weld with shielding gas ensures that the underside of the weld is
protected from atmospheric elements and can be done with commercial
apparatuses or individually manufactured methods.
Finally, remember to maintain adequate post-flow. The best practice is
to maintain one second of post-flow for every 10 amps of welding
current used during welding.
Avoiding Distortion and Cracking.
Because stainless steel is prone to greater thermal expansion than
other materials it tends to distort easily. Too high of a current
setting and/or too slow of travel speeds contribute to this problem.
Thermal expansion occurs because the HAZ (heat affected zone) on
austenitic stainless steel is more localized than with other
materials. When the weld cools, there is slow thermal transfer to the
surrounding material that can lead to buckling. By clamping or using a
fixture, especially on thin gauge material, you can reduce the chances
of buckling
Along with distortion comes the potential for cracking, By using a
joint design consisting of a V-grove, modified V-grove, U-grove of a
J-grove that limits the number of weld passes and the amount of heat
applied the chance of cracking will be reduced. Cracking will also
occur in the weld initiation and crater area. One way to prevent
cracking in this area is to use run-on/run-off tabs. These tabs need
to match the base material for the best results. The tabs provide an
area to ‘run-on’ or ‘run-off’ the weld thus eliminating arc starting
and craters on the actual weld joint and can be easily ground or cut
off-after the weld cools
Remember: even with the right type and amount of gas, good heat input
and proper travel speeds, training and practice is still the best
defense against the pitfalls of TIG welding austenitic stainless
steels.
Notice the narrow heat affected zone (HAZ) created by high speed
pulsed TIG, which helps preserve the metal’s original properties.
The Art of TIG Welding
When TIG welding stainless there are a few points to keep in mind to
achieve a cosmetically appealing and sound weld. Because stainless
steel does not adequately dissipate heat, maintaining proper heat
input when welding is critical. Too much heat can lead to warping,
embrittlement or rust. As little as five amps too much can damage
stainless steel’s properties. There are, however, several ways to
control heat input:
Good fit-up: Adding filler metal to fill gaps puts more heat into the
part, so good fit-up is important. It’s impossible to add a lot of
filler metal and keep energy out of the part.
The correct filler metal: The filler metal diameter should be thinner
than the base metal. If it’s thicker than the base metal, too much
heat is needed to melt the filler metal. The filler metal should also
match the base metal alloys in order to maintain consistent mechanical
and corrosion properties.
Stainless Steel
Filler Rod Used
Stainless Steel
Filler Rod Used
301
308
310S
310
302
308
314
310, 312
302S
308
316
316
304
308
316L
316
304L
308
317
347
305
308, 310
321
347
308
308
330
347
309
309
347
347
309S
309
348
347, 348
310
310
Choose the right tungsten size: You can’t weld precisely on 1/16-in.
material with a 1/8-in. tungsten. Use the right tungsten diameter
based on your amperage. See page 7 for the proper size.
Use the correct tungsten geometry: The tungsten’s shape plays a role
in the weld’s width and penetration. In welding stainless steel, the
sharper the tungsten, the wider and less penetrating the bead will be.
On a sharper point, (ground to a taper length that is more than 2½
times the electrode diameter), the arc tends to fan out, creating a
wider heat affected zone. With a blunter point (less than 2.5 times
the electrode diameter), the arc comes straight down with less flaring
for a deeper, thinner bead and thinner heat affected zone.
Use a fingertip or foot control: You need to be able to start the arc
and adjust the amperage from the beginning to the end of the weld. Set
the welder to the desired amperage, which should be just a bit more
power than you’ll need. If your welder is fairly accurate, you’ll only
need to adjust the fingertip or foot control a little bit to adjust
welding output.
Start with low amperage and allow the puddle to form: Then back off
two or three amps and add filler.
Maintain the correct puddle size: The weld puddle should be the
thickness of the base metal. If the puddle grows too large, turn down
the heat.
Eliminate craters by easing down the current at the end of the weld
and adding filler metal until the puddle solidifies. Use your torch’s
fingertip or foot pedal control or your welder’s sequencer.
Keep the gas flowing and directed at the puddle until the orange color
fades. The post flow also cools the puddle and the tungsten. Moving
the torch too fast can blow gas away from the tungsten, turn it black
and make it more difficult to start next time.
Use pulsing. To control heat input, use a welder with DC pulsing
capabilities. In pulsing, the current transitions between a high peak
amperage and a low background amperage that maintains the arc but
allows the puddle to cool. The peak current provides good penetration,
but the background current allows the weld puddle to cool slightly,
preventing warping, embrittlement and carbide precipitation.
Pulses per Second (PPS): Is simply how many times the machine will
complete one pulsing cycle in a time span of one second. Increasing
the number of pulses per second produces a smoother ripple effect in
the weld bead, narrows the weld bead. Reducing the number of pulses
per second widens the weld bead. Pulsing also helps agitate the puddle
and release any porosity or gas trapped in the weld.
Some beginning TIG welders use a slow pulsing rate (perhaps .5 to 1
PPS) to help them develop a rhythm for adding filler metal. For
welding carbon or stainless steel, use a rate of 100 to 500 PPS. Start
at 100 and work upward. Higher pulsing (generally above 100 pulses per
second) increase puddle agitation, which in turn produces a better
grain molecular structure within the weld. High speed pulsing also
constricts and focuses the arc. This increases arc stability,
penetration and travel speeds, and it produces a smaller heat-affected
zone.
Table 2: Austenitic, Super-Austenitic and Duplex Stainless Steel
Alloys
Base Metal
304L
304H
316L
317L
904L
6% Mo SS
7% Mo SS
Alloy 20CCb-3
2304 Duplex
2205 Duplex
Carbon and Low Alloy Steel
ABC
ABC
ABC
ABC
ABC
ABC
ABC
ABC
N
N
Type 304 SS
D
DE
DF
DG
DC
C
C
DCH
NL
NL
Type 304H SS
E
EF
EG
*
*
*
ECH
*
*
Type 316L SS
FG
FG
FC
FC
FC
FCH
NL
NL
Type 317L SS
GC
GC
GC
GC
GC
L
L
Type 904L SS
C
C
C
C
L
L
Type 6% Mo SS Eg: 254 SMO, AL 6XN
CJK
CJK
*
*
*
Type 7% Mo SS Eg: 654 SMO
CJK
*
*
*
Type Alloy 20Cb-3
H
*
*
Type 2304 Duplex SS
LM
LM
Type 2205 Duplex SS
LM
Legend Notes:
A) AWS A 5.4 Classification E309L-XX
B) AWS A 5.11 Classification ENiCrFe-2 or -3
(-2 is Alloy 718 and -3 is Inconel 182)
C) AWS A 5.11 Classification ENiCrMo-3
(Inconel 625)
D) AWS A 5.4 Classification E308L-XX
E) AWS A 5.4 Classification E308H-XX
F) AWS A 5.4 Classification E316L-XX
G) AWS A 5.4 Classification E317L-XX
H) AWS A 5.4 Classification E320LR-XX
J) AWS A 5.11 Classification
ENiCrMo-4(Hastelloy C-276)
K) AWS A 5.11 Classification ENiCrMo-11
(Hastelloy G-30)
L) AWS A 5.4 Classification E2209-XX
M) AWS A 5.4 Classification E2553-XX
N) AWS A 5.4 Classification E309MoL-XX
* Unlikely combination
1. Table 2 refers to coated electrodes only. For bare wire welding
(GMAW, GTAW), use equivalent electrode classification (AWS A 5.14)
2. There are many proprietary alloys available in the market and
material combinations you might encounter. Consult the manufacturer or
the DSF for proper filler metal selection
TIG (GTAW) Calculator, Stainless Steel
Work
Thickness In.
Weld
Tungsten
Electrode Dia.
Cup
Orifice Dia.
Filler
Rod Dia.
Current
Flat Welding
Gas
Speed
in/min
Remarks
Type
No.
Type
Amps
Type
Flow
PSI
Stainless Steel
Manual Welding Straight Polarity
D.C.
For Mild Steel, Use
10% Higher Amperage Values
1/16
Butt
1
1/16
1/4-3/8
1/16
DC
50-80
Ar
11
20
12
Lap
4, 5
1/16
1/4-3/8
1/16
DC
60-90
Ar
11
20
10
Corner
6, 7, 9
1/16
1/4-3/8
1/16
DC
50-80
Ar
11
20
12
Fillet
10
1/16
1/4-3/8
1/16
DC
60-90
Ar
11
20
10
3/32
Butt
1
1/16
1/4-3/8
1/16 or 3/32
DC
80-100
Ar
11
20
12
Lap
4, 5
1/16
1/4-3/8
1/16 or 3/32
DC
90-120
Ar
11
20
10
Corner
6, 7, 9
1/16
1/4-3/8
1/16 or 3/32
DC
80-100
Ar
11
20
12
Fillet
10
1/16
1/4-3/8
1/16 or 3/32
DC
90-120
Ar
11
20
10
1/8
Butt
1
1/16
1/4-3/8
3/32
DC
85-120
Ar
11
20
12
Lap
4, 5
1/16
1/4-3/8
3/32
DC
100-140
Ar
11
20
10
Corner
6, 7, 9
1/16
1/4-3/8
3/32
DC
85-120
Ar
11
20
12
Fillet
10
1/16
1/4-3/8
3/32
DC
100-140
Ar
11
20
10
3/16
Butt
1
3/32
1/4-3/8
1/8
DC
125-200
Ar
13
20
10
Lap
4, 5
3/32
1/4-3/8
1/8
DC
150-200
Ar
13
20
8
Corner
6, 7, 9
3/32
1/4-3/8
1/8
DC
150-200
Ar
13
20
10
Fillet
10
3/32
1/4-3/8
1/8
DC
175-225
Ar
13
20
8
1/4
Butt
1, 2
1/8
1/2
3/16
DC
225-300
Ar
13
20
5
1 or 2 passes
Lap
5
1/8
1/2
3/16
DC
250-325
Ar
13
20
5
1 or 2 passes
Corner
6, 7, 8
1/8
1/2
3/16
DC
250-300
Ar
13
20
5
1 pass
Fillet
10
1/8
1/2
3/16
DC
250-320
Ar
13
20
5
1/2
Butt
2, 3
1/8 or 3/16
1/2
1/4
DC
300-400
Ar
15
20
2 or 3 passes
Lap
5
1/8 or 3/16
1/2
1/4
DC
325-425
Ar
15
20
3 passes
Corner
8
1/8 or 3/16
1/2
1/4
DC
325-425
Ar
15
20
3 passes
Fillet
10
1/8 or 3/16
1/2
1/4
DC
325-425
Ar
15
20
3 passes
NOTES: Reduce currents 10% to 20% for vertical and overhead. Ceramic
or glass cup should be used for currents to 250 amps. Water-cooled cup
should be used for currents above 250 amps.
Types of Tungsten Electrodes
Pure, (Green). Good arc stability on AC current, with either balanced
wave or continuous high frequency stabilization. Preferred for AC
welding of aluminum and magnesium. When heated, the pure tungsten
electrode forms a balled end.
2% Ceriated, (Orange). The most abundant of the rare earth elements.
These are all-purpose electrodes that will operate with AC or DC of
either polarity. Provide long life and high current-carrying capacity.
Unlike Thoriated, Ceriated is not a radioactive material.
1% Lanthanum, (Black), Often refereed to as Lanthana, another of the
rare earth elements. The operating characteristics are very similar to
the Ceriated electrode.
2% Thoriated, (Red), 1% Thoriated, (Yellow), Designed for DC
applications. Thoria content is dispersed evenly throughout their
entire length. Maintains a sharpened point well, which is desirable
for welding steels. Good are starting and high current carrying
capacity. Thoria content is responsible for increasing the life of the
electrode.
Zirconium, (Brown), Designed for AC welding when the highest quality
work is necessary. Contains less than 1% zirconium oxide, which
produces a very stable arc. Current carrying capacity equal to or
greater than equal-sized thorium electrode. Not recommended for DC
welding.
Gauge to Decimal to Millimeter Conversion Chart
Gauge
( ga. )
Standard Steel Thickness
Galvanized Steel Thickness
Aluminum Thickness
inch
mm
inch
mm
inch
mm
3
0.2391
6.08
0.2294
5.83
4
0.2242
5.71
0.2043
5.20
5
0.2092
5.32
0.1819
4.61
6
0.1943
4.91
0.1620
4.13
7
0.1793
4.55
0.1443
3.67
8
0.1644
4.18
0.1285
3.25
9
0.1495
3.78
0.1532
3.89
0.1144
2.90
10
0.1345
3.42
0.1382
3.52
0.1019
2.57
11
0.1196
3.01
0.1233
3.13
0.0907
2.29
12
0.1046
2.65
0.1084
2.74
0.0808
2.05
13
0.0897
2.27
0.0934
2.36
0.0720
1.85
14
0.0747
1.89
0.0785
2.00
0.0641
1.63
15
0.0673
1.71
0.0710
1.81
0.0571
1.45
16
0.0598
1.50
0.0635
1.62
0.0508
1.27
17
0.0538
1.35
0.0575
1.45
0.0453
1.16
18
0.0478
1.21
0.0516
1.31
0.0403
1.02
19
0.0418
1.05
0.0456
1.16
0.0359
0.90
20
0.0359
0.90
0.0396
1.00
0.0320
0.81
21
0.0329
0.82
0.0366
0.93
0.0285
0.73
22
0.0299
0.75
0.0336
0.86
0.0253
0.65
23
0.0269
0.68
0.0306
0.76
0.0226
0.57
24
0.0239
0.59
0.0276
0.70
0.0201
0.51
25
0.0209
0.52
0.0247
0.63
0.0179
0.46
26
0.0179
0.46
0.0217
0.55
0.0159
0.39
27
0.0164
0.42
0.0202
0.52
0.0142
0.37
28
0.0149
0.37
0.0187
0.47
0.0126
0.32
29
0.0135
0.35
0.0172
0.44
0.0113
0.30
30
0.0120
0.31
0.0157
0.39
0.0100
0.26
31
0.0105
0.27
0.0142
0.36
0.0089
0.22
32
0.0097
0.25
0.0134
0.34
0.0080
0.20
33
0.0090
0.23
0.0071
0.18
34
0.0082
0.20
0.0063
0.16
35
0.0075
0.19
0.0056
0.14
36
0.0067
0.17
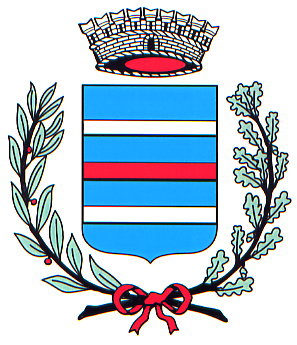

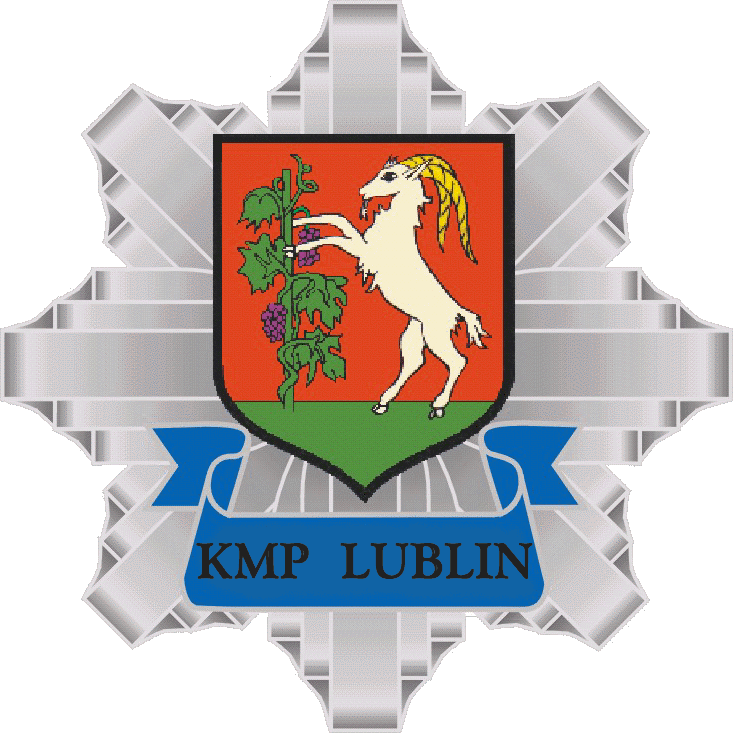

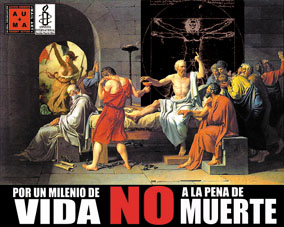

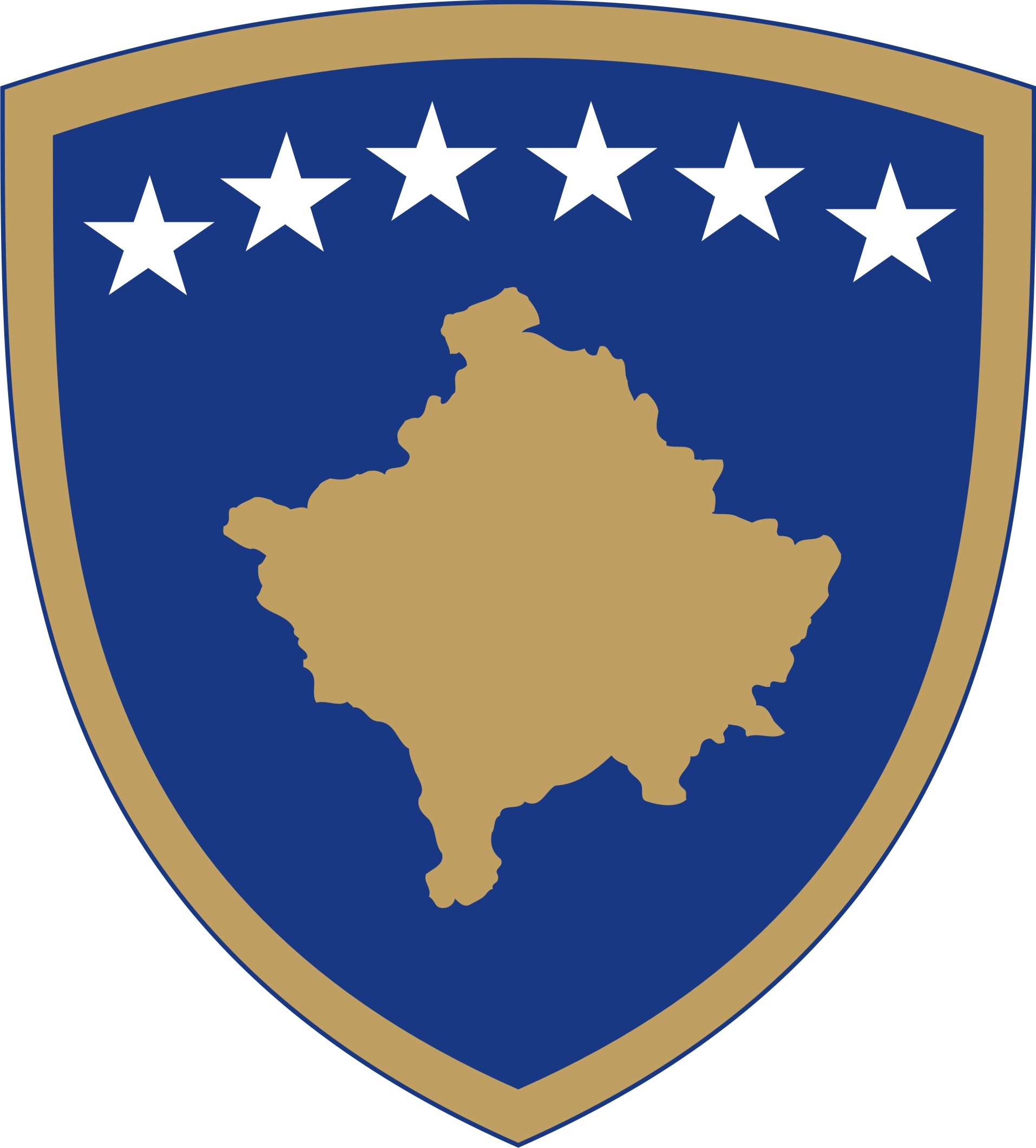
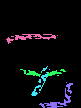
